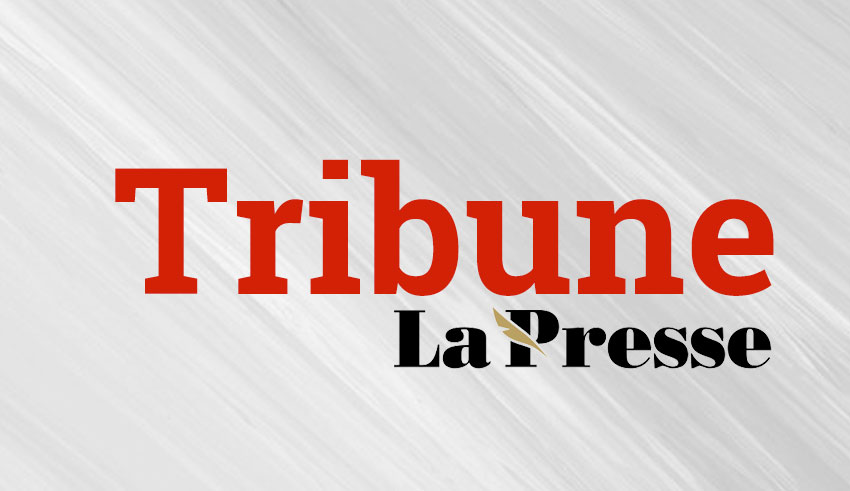
Par Halila Taoufik et Mohamed Férid Herelli
La maintenance des équipements, tous secteurs confondus, en Tunisie représente près de 40% de toutes les activités publiques et privées (coûts directs et indirects) et, dans quelques cas, pourrait atteindre 60% ce qui a un impact direct et indirect sur notre économie en général et notre tissu industriel en particulier dont le résultat de sa mauvaise gestion est la perte de la compétitivité de nos produits et services à l’échelle internationale.
La maîtrise du processus de management de la maintenance est le plus souvent négligé par les responsables et ne constitue pas une priorité car elle est souvent gérée au hasard aussi bien sur le plan financier que technique.
En l’absence de chiffres actualisés, et selon le constat au quotidien de notre parc industriel immobilisé, la Tunisie est devenue «Un cimetière d’équipements usagés».
C’est ainsi qu’il y a lieu de rappeler qu’en 1986, le Cetime a pris l’initiative d’organiser, pour la première fois, le Sapri «Salon de la pièce de rechange industrielle», qui a regroupé les grands donneurs d’ordres et industriels, dans le but d’étudier les possibilités d’intégration et fabrication locale des pièces de rechange industrielles sous toutes leurs formes. Ainsi et vu la périodicité de la tenue de ce salon pendant quelques années il y a eu la création de plusieurs PME/PMI qui se sont bien adaptées aux demandes spécifiques des grands donneurs d’ordres ce qui leur a permis d’avoir une activité pérenne et de développer leurs productivités à travers l’innovation et la mise au point de nouvelles solutions liées à des processus technologiques complexes et avancés.
Par ailleurs, et grâce à ce salon , plusieurs entreprises industrielles publiques et privées ont pu améliorer leurs systèmes d’information de gestion et de pilotage des stocks ce qui a induit une disponibilité permanente et fiable de l’outil de production, surtout à travers la maintenance préventive et curative, et la veille aux innovations technologiques dans ce domaine d’activité (mises à jour des bases des données des pièces de rechange, des processus , du choix rationnel des fournisseurs…) ce qui a réduit les dégâts et les pertes de la production et de la productivité de nos entreprises et surtout en ce qui concerne les points suivants :
1 / Le temps d’arrêt
Un équipement peu fiable peut entraîner des temps d’arrêt, ce qui provoque l’arrêt de la production pendant une période indéterminée (de plus, cela se produit souvent sans avertissement). Le coût réel d’une panne d’une machine est estimée entre 4 et 15 fois le coût de son entretien sans compter les pertes subies suite au non-respect des délais envers les clients.
2 / Le remplacement de l’équipement
Lorsqu’il s’agit d’un équipement peu fiable, il faut tenir compte de la probabilité de le remplacer et prévoir un budget pour cette action ; or, ce qui est constaté, et surtout dans les entreprises publiques, généralement ces dernières ne prévoient pas de tels budgets ce qui les oblige en cas de problème à exploiter d’autres lignes de budget de gestion annuel destiné à d’autres activités ce qui constitue une faute de gestion et de gouvernance inacceptable
3/ Impact sur la qualité
Des équipements de production mal entretenus et non étalonnés ont des conséquences directes sur la qualité des produits ce qui constitue une perte aussi bien de la compétitivité que de clients, ce qui ramène à l’importance de respecter les délais d’étalonnage et calibrage des instruments de mesure à travers la chaîne de métrologie industrielle et scientifique.
4/ Les risques pour la sécurité et l’environnement
Des équipements de production non fiables pourraient mettre en danger aussi bien le personnel de la production que les clients surtout au niveau final de contrôle (un équipement d’inspection défaillant, par exemple, peut laisser passer des contaminants sans les détecter, ce qui met le personnel de production, les consommateurs et l’environnement en danger)
Par ailleurs, nous constatons que des tonnes de reste des chantiers (grues, bus…) laissés en terre en tant que ferrailles ont des conséquences désastreuses sur la nappe phréatique par l’injection des résidus des métaux lourds.
Pour prévenir tous les problèmes indiqués et suivant les expériences à l’échelle nationale et internationale, il est recommandé ce qui suit :
1/ Développer les sciences de la maintenance dans nos écoles d’ingénieur et facultés scientifiques et développer une telle culture dans nos unités de production
2/ instaurer une réglementation obligatoire pour effectuer les opérations de maintenance préventive par le personnel interne de l’entreprise ou à travers le recours à la sous-traitance et y répondre administrativement et pénalement en cas de non-respect de cette réglementation,
3/ Les tâches d’entretien de base requises peuvent être effectuées par les opérateurs eux-mêmes, tandis que les inspections, services et tests de routine peuvent être réalisés par des sous-traitants confirmés, ce qui pourrait encourager nos jeunes diplômés à créer leurs propres entreprises dans de tels domaines d’activité.
4/ Implanter obligatoirement dans chaque unité de production, tous secteurs confondus, des applications Gmao (Gestion de la maintenance assistée par ordinateur)
5/ Appeler le ministère de l’Industrie à encourager la reprise de l’organisation périodique du Sapri avec au programme des événements liés à la co-traitance et faire connaître notamment les nouvelles potentialités technologiques de chaque secteur.
6/ Encourager la coopération entre l’université, les écoles d’ingénieur et le monde industriel pour plus d’ouverture afin de toucher de près ce domaine et donner à nos futurs diplômés les potentialités d’innover et d’apporter des solutions basées sur les nouveautés technologiques à savoir, la fabrication additive, le prototypage rapide, l’industrie 4.0…)
H.T, Président de la chambre nationale des intégrateurs des réseaux télécoms (Cnirt)
M.F.H, Ancien Directeur général du Cetime
Expert-Consultant en développement industriel